
We are living in the future.
It’s easy to ignore all of the technological advancements in society. That’s what happens when you live beside them every day. It becomes easy to overlook them.
Artificial Intelligence, machine learning, algorithms, and even robots are accomplishing jobs done by humans. Some people think it’s a bad thing. But, if there’s ever a serious labor shortage, we need all the help we can get.
One of the industries where robots are making the biggest impact is in the manufacturing space. Warehouse and inventory tasks are starting to be handed off to robots. These particular types of robots are called autonomous mobile robots.
But, what are autonomous mobile robots? Autonomous mobile robots in the workplace may be a new concept to you. If they are, that’s ok. We’re here to clue you in on everything you need to know regarding autonomous mobile robots.
We’ll talk about what leveraging their automated labor can do for your operations management. Finally, we’ll discuss some leaders in the space and go over the products that they’re offering.
By the time you’re done reading, you’ll be your team’s resident autonomous mobile robot expert. But, there’s a lot of information to cover.
Let’s get going!
What Are Autonomous Mobile Robots (AMRs)?
Autonomous mobile robots are robots that involve a complex system of electronics and computer programming. Because these robots are so complex, they are able to complete tasks a human would do. They also have the ability to complete these tasks on their own.
Once a robot knows its job, that’s it. Automation engineers can set the robot to work and it will continue to do its job with very little monitoring.
Leveraging this technology has a lot of benefits for manufacturing companies. These benefits can then be passed along to you, the customer.
Although there may be people that disagree with the growing use of robots and AI, the end result is a net positive for everyone involved.
Life Before AMRs
AMRs can be a big improvement in a manufacturing setting. The parts and inventory companies store in warehouses gives these robots plenty to do.
AMR technology is not something that’s brand new. Companies within the manufacturing industry have been leveraging automation technology for decades. This automation has come in the way of long lines of conveyor belts and automated guided vehicles (AGVs).
Leaders within the manufacturing industry are optimistic that AMR technology can improve upon the current automation. Manufacturing companies see AMRs as an improvement because they require less clumsy technology than their predecessors.
Long lines of conveyor belts spanning the entire length of a warehouse or factory can be bulky. They can take up so much room that they make conducting business difficult for the warehouse team.
AGVs are no different. They may no take up as much room, but they require additional equipment to work properly. Manufacturing warehouses need wire strips or magnetic tracks on the floor to help guide the AGV’s path.
If an AGV gets off-track for some reason, it needs to be corrected. Otherwise, it may constantly be running into the wall like your Roomba vacuum at home.
How Are AMRs Different?
AMRs can accomplish more than conveyor belts and AGVs without as much of the extra technology. This is because AMRs operate on an advanced system that leverages LIDAR technology.
LIDAR technology works by using light detection and ranging. AMRs use LIDAR along with their other onboard technology to navigate through a warehouse or factory environment. They can find their way through the workplace just like a human can.
This is because, in addition to LIDAR, AMRs have their own onboard collision detection and intelligence systems. Much like us, AMRs are able to choose the best route to a destination every time. And it’s all because of these systems.
Benefits of AMRs
Starting to leverage the technology of AMRs can really transform a manufacturing company’s workflow. AMRs have several other benefits, as well.
Using AMRs requires much less infrastructure. As a result, manufacturing companies experience significant cost savings that directly affect their bottom line. AMRs can be expensive. Knowing that they are going to offer an immediate return on investment makes pulling the trigger to purchase one much easier.
In addition to cost savings, AMRs can help manufacturing teams maximize the space in their warehouses or factories. There are no magnetic tracks or wire strips necessary for AMRs. This allows warehouse managers to focus on configuring their shelving in a way that works best for the company.
Conveyor belts and AGV tracks no longer have to dictate the company’s warehouse layout.
The Future of Manufacturing
Another benefit AMRs provide is allowing companies to keep up with the latest trend in manufacturing. That trend is adaptive manufacturing.
Rising real estate prices are causing plant, warehouse, and factory space to become much more expensive. As a result, manufacturing companies need to do the best they can with what they’ve got. This makes the need for adaptive manufacturing higher now than ever before.
AMRs allow companies to design their floorplans efficiently. They can really shrink the size of their layout and make changes on the fly. Companies that can grasp this concept and put it to work will be miles ahead of their competition.
In addition, certain industries need to adapt to new shipments on the fly. Certain industries have to implement adaptive manufacturing based on their shipments. One such industry is consumer electronics.
These businesses have new inventory coming in every couple of weeks, or even every couple of days. Without the help of AMRs, they wouldn’t be able to adapt to this frequency of shipments.
Companies would be left applying and reapplying magnetic tracks for their AGVs to accommodate each shipment. With AMRs, warehouse managers can simply rely on the robot’s programming and allow it to find the best route on its own.
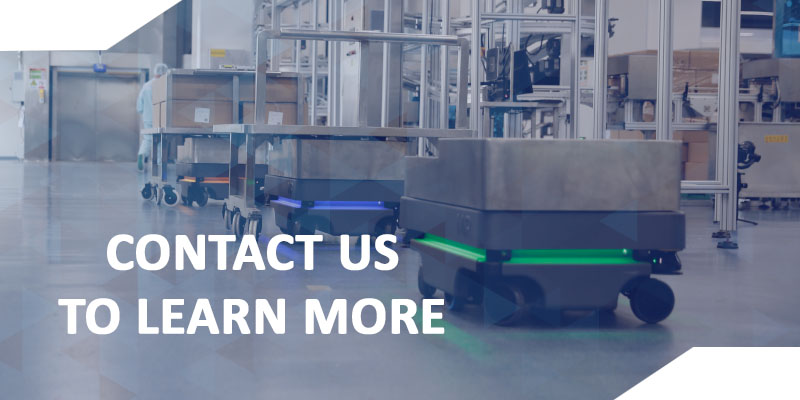
Challenges Facing AMRs
It’s easy to see the many benefits using AMRs can provide. However, industries like manufacturing are dragging their feet with AMR adoption. One of the reasons is that manufacturing is a historically risk-averse sector of the economy.
Upper-level managers of many manufacturing companies see the benefit of using mobile industrial robots. The problem, however, is they’re afraid of adopting the technology too soon. Using the technology before the industry is “ready for it” could result in significant revenue losses for the company.
Most companies also struggle with the price tag for AMRs. It’s not so much the price tag, but the fact that they’re paying a lot of money for a robot that can only perform one task. As a result, the AMR industry is moving toward creating robots with multi-modal functionality.
One such company is Mobile Industrial Robots (MiR). Automation engineers at MiR are working on AMRs that can accomplish multiple functions within the manufacturing space. The hope is that providing a robot that’s able to accomplish more than one task will justify the upfront costs.
MiR hopes to do this using a unique “plug and play” design. Where other AMR companies offer general use robots, MiR plans to offer a robot that focuses on integration. MiR’s new multi-modal robot will integrate with other pieces of hardware to help you get more done.
Think of the robot as a “blank slate” that can adapt to whatever tasks are necessary.
MiR’s Latest AMR Products
With that theme in mind, MiR is beginning to launch two new AMR products. These new robots are generating a lot of buzz within both the AMR and manufacturing communities. The new models are the MiR600 and the MiR1350.
Let’s take a look at what they can accomplish for you and your team.
MiR600 Facts and Features
The MiR600 is one of the safest robots around. It complies with all of the highest safety standards within the industry. It’s also been engineered to handle any fluids, dust particles, or debris your warehouse can throw at it.
The MiR600 has the ability to “see” completely around itself. This AMR misses nothing thanks to its 360-degree vision capability. The robot’s vision also extends as high as two meters above the ground.
Another amazing feature is the robot’s autonomous navigation. The MiR600 can find the best route to its destination all on its own. On its way to its destination, it will maneuver safely and effectively. Warehouse managers can also load palettes onto this robot with ease.
The MiR600’s flexibility and user-friendly features make it one of the leading AMR products in the industry.
MiR1350 Facts and Features
The MiR1350 boasts all of the features of the MiR600 and much, much more. This cutting-edge robot can handle heavier payloads within your factory or warehouse. The MiR1350 can handle payloads weighing up to 1350 kg or 3,000 pounds.
You can rely on the MiR1350 to literally do your heavy lifting.
The MiR1350 has the same autonomous navigation, safety, vision, and longevity as the MiR600. It also can be fitted with special palette lifters provided by MiR. With these palette lifters, the MiR1350 can replace any standard palette loader or truck.
Engineers can operate both robots from their smartphone, tablet, or computer. MiR’s operation interface is user-friendly and allows for amazing ease of use. There isn’t much of a learning curve with MiR’s newest technology.
You’ll have your robots up and running quickly, putting in an honest day’s work on the warehouse floor in no time.
AMRs and the Current Labor Shortage
Another area where AMRs can help manufacturing and industrial teams in the current labor shortage.
As we mentioned earlier, some people are afraid of robots like AMRs taking their jobs. But, in manufacturing, the jobs being done by robots haven’t been done adequately by humans anyway.
Companies are seeing startling numbers of absences from their human workforce. In fact, one industry leader reported as much as 25% of their workforce being absent on any given shift. This can severely reduce the effectiveness of your production line.
This is all the more reason for companies to leverage AMR technology. Even if a large portion of your human workforce is absent, your company’s downtime would still be limited. AMRs can step in and pick up where the human team left off.
AMRs can also help in a labor shortage by drastically reducing the number of employees necessary. AMRs can handle the heavy lifting both literally and figuratively. They can move your heaviest palettes, but they can also assume the responsibility of the mundane day-to-day tasks.
Using AMRs for the small stuff will allow your human team to focus on the more high-value, high-dollar tasks.
It may take a little training, but your warehouse staff will quickly become familiar with working with these autonomous mobile robots. Training your employees to work with these robots will also help your workforce.
If an employee on your team can become a skilled operator of AMRs, it’s another skill they can add to their resume. Adding marketable skills to their toolbelt is one of the best moves human employees can make during a labor shortage.
Robots to the Rescue
There you have it! Everything you need to know about autonomous mobile robots. We hope you enjoyed this article and came away with a new perspective.
AMR technology can do a lot to grow your business and help your team thrive through the current labor shortage.
Our team at RG Group offers a wide variety of AMRs including the latest products from MiR. If you have any questions or are looking to start implementing AMR technology in your business, contact us today.
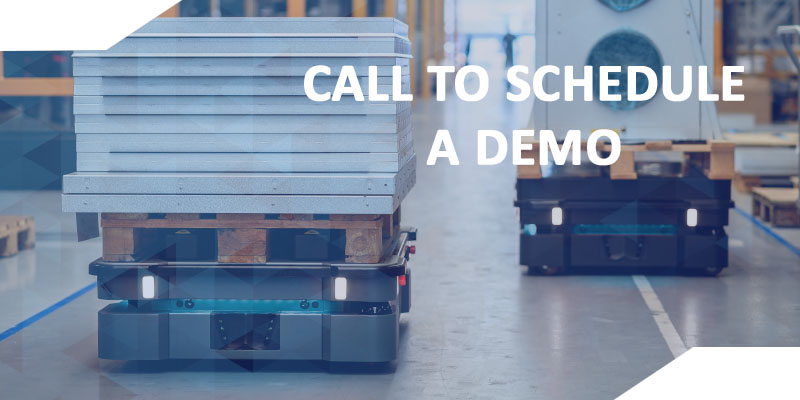